The past decade has seen a major evolution in engine and transmission technology, and moving forward, automakers will continue to look for greater powertrain efficiency in order to meet stricter fuel efficiency and emissions standards. To meet the rising consumer demand for engines that burn fuel more efficiently, global automotive OEMs and their tiered suppliers are manufacturing smaller, lighter engines and other powertrain components. The increased availability of lightweight materials like aluminum and carbon fiber has made a more fuel efficient but still powerful design possible – even for high-load, harsh environment powertrain applications.
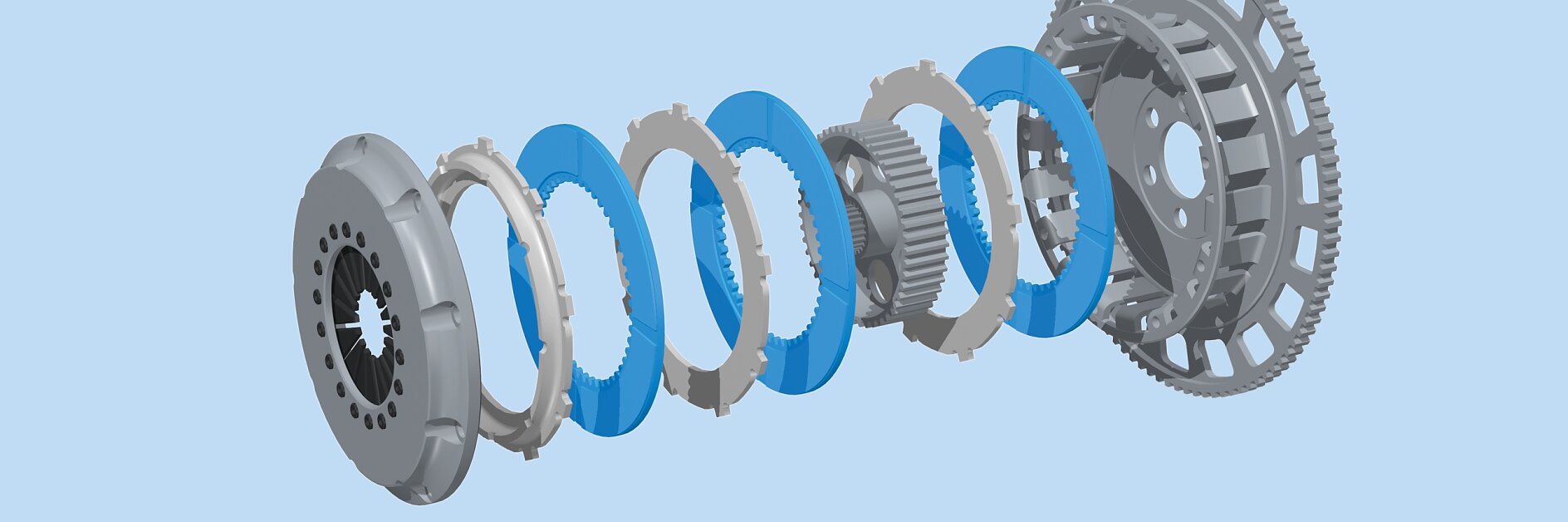
Our Heat Activated Film (HAF) – Designed for the Harshest Powertrain Applications
Technologies
To help automotive OEMs and their tier suppliers develop new powertrain innovations, tesa's Heat Activated Film (HAF) has been designed and tested for extreme bonding requirements that call for superior resilience, chemical resistance, and very high bonding strength.
As the Drive to Downsize Continues, Automotive Engineers Develop New Ways to Lighten the Powertrain
A High Performance Adhesive Solution for Bonding High Performance Materials
New cars and trucks certainly look different on the outside than they did 10 years ago, but the biggest changes are now happening under the hood. In order to ensure an adequate energy flow in smaller powertrains, auto makers have begun to use advanced materials in everyday vehicles.
For example, carbon fiber is an ideal high performance friction layer on synchronizer rings for manual and dual-clutch transmissions. These carbon fiber friction linings also show an excellent oil compatibility and a high gear shift comfort, which ensures a long powertrain lifecycle.
The Proven Benefits of tesa HAF®
Until now, metal replacement in vehicles has typically focused on lower-load parts, but in order to incorporate these new lightweight materials into higher-load, harsher-environment applications, manufacturers need a more reliable and rugged method of structural bonding.
With an adhesive layer that contains nitrile rubber and a phenolic resin, tesa HAF® solutions function as thermosetting adhesive tape. When heated, a chemical reaction is started that creates a securely bonded system. Once fully cured, the heat activated film adhesive does not go back to its original status when re-exposed to heat.
This also offers high chemical resistance to engine oil and solvents and a high cohesiveness at frictional heat (up to 350°C). tesa HAF® bonds very well to steel and carbon fiber, which makes it an excellent solution for bonding carbon fiber linings to synchronizer rings, but the potential of this next-generation bonding solution is not limited to a vehicle’s transmission. Other proven applications include bonding carbon fiber to clutch discs, mounting sensor plates for gear control, and brake shims to brake pads.
Proven benefits of tesa HAF®
- Extremely high bonding performance up to 30 N/mm²
- High resilience
- High cohesiveness at frictional heat
- High chemical resistance against engine oils
- Long-term stability at high load
- Even and precise bonding
- Precise application die-cuts
- A fast, clean, cost-effective process
Helping Generate More Power from Less Space
As the automobile industry continues to look for new ways to decrease displacement while maintaining power output, the need for alternatives to glue and mechanical bonding methods will continue to grow. Our thermosetting adhesive tapes are a proven solution to the industry’s greatest bonding challenges. With its resilience, chemical resistance, and high bonding strength, HAF has been especially designed for situations where new designs and ideas are creating compact lightweight designs that reduce emissions and fuel consumption. When combined with advanced materials like aluminum and carbon composites, tesa HAF® offers automotive OEMs a unique set of synergies to help them pursue greater levels of fuel efficiency and customer satisfaction.