The Great Tape Debate: Answering the 5 Most Common Plate Mounting Tape-Related Questions
At 2023's FTA Forum event, our resident expert, Alix Guyot, was asked to participate in a panel discussion called The Great Tape Debate. Alix is an Application Solution Engineer for the Flexo, Print & Paper division at tesa tape and has over 12 years of experience in the flexo printing industry. She is currently serving as Chair of the FTA Excellence in Flexography committee and is FIRST Implementation Specialist Level 3 certified. During the debate, the panelists were asked to respond to live audience survey results related to a variety of plate-mounting topics. We’ve compiled Alix’s professional advice for your reference below.
As a general rule, how many different tape options do you think a print shop should have available to optimize for typical applications? Does this answer change based on market segment?
This will depend on the range of linescreens you use, the range of graphics you print, and the type of plates or surface screening you use. I would say more and more printers can use two to three tapes: one soft tape for screens, one hard tape for solids, and one helper tape either softer or harder. Typically, when I see customers using a lot of different densities, it’s being press operator-driven and not process control-driven. One exception to this is when a single plant uses a wide variety of substrates including film and highly textured papers. In this case, it may be necessary to evaluate the tape per substrate category. However, I would still highly recommend standardizing per substrate type.
What is the recommendation for changing tapes or self-adhesive sleeves? Are there any indicators to be aware of that show a change should be made?
We recommend changing the tape between every job. The problem with reusing tape is that there is often no process control behind it. If you reuse tape, are you tracking how many times you have reused it and how many impressions have been printed on that tape? What if the tape was damaged on press from hard impression — are the press operators communicating that to the team that is remounting on the tape? Because of these variables, we do not recommend reusing tape.
What considerations should be made when mounting and demounting plates from the tape or self-adhesive sleeves?
When mounting remember that the adhesive is pressure sensitive, especially when handling your low tack adhesives. So, any area of the tape or plate that gets less pressure — or worse, no pressure — will not stick. These areas are where air bubbles will begin to form. The bad news is, any area that doesn’t stick well at the beginning can grow bigger, as the tape will pull up areas around it.
When demounting, work with your supplier to optimize technique. Low tack adhesives respond better to quick movements and high tack adhesives remove better with steady pressure. Ask to find out what you have. Also, we recommend pulling from the corners when demounting tapes or plates. This allows you to reduce the effort needed to demount.
What variables do you see that have the biggest impact on tape or self-adhesive sleeve performance when trying to standardize across multiple sites? What are some strategies to mitigate these variables, or to compensate for the inherent differences?
Application is often the biggest variable. Automatic mounters have really helped standardize this, but they are often used for the plate only. Techniques in how the tape or plate is applied, from amount and type of pressure to how much tension is on the tape, can impact how the tape performs. Another big factor is sleeve or cylinder condition. If the sleeves have more cuts than solid area, the tape has nothing to stick to. You can have the same sleeves in multiple locations, but how well they are maintained is critical.
If you are struggling with this, start by capturing the actual mounting steps taken at each location and shift. Not what’s written and not what the mounters say they do, but what they actually do. Often, you’ll find that it is not the same process between each plant. Once you know where the differences are, you can work to train the various shifts. tesa is a great resource for this. Through our plate-mounting certification, we’ll spend time with your mounters to find the variation and then work with your teams to get everyone on the same page.
What main characteristics differentiate using mounting tapes versus self-adhesive sleeves, and is there room for both at a print facility?
The biggest difference (after not having to mount tape) is that the self-adhesive sleeves have less durometers. This isn’t a bad thing, as more and more printers use only 2 durometers, but it requires optimization to get there. Because the tesa® Twinlock composition utilizes a much thicker foam than traditional plate-mounting tape, it has a much larger print latitude. This means that you can accomplish more with one durometer tesa® Twinlock than you can with plate-mounting tape. This thicker foam quality can also help compensate for a large amount of bounce.
I think there is absolutely room for both mounting tape and self-adhesive sleeves. At tesa, we recommend a hybrid approach customized to your individual requirements. Start by transitioning your most common repeats to tesa® Twinlock sleeves to see the ROI realized faster.
Stay tuned for part two of this series, where we address the unanswered audience questions from the live event!
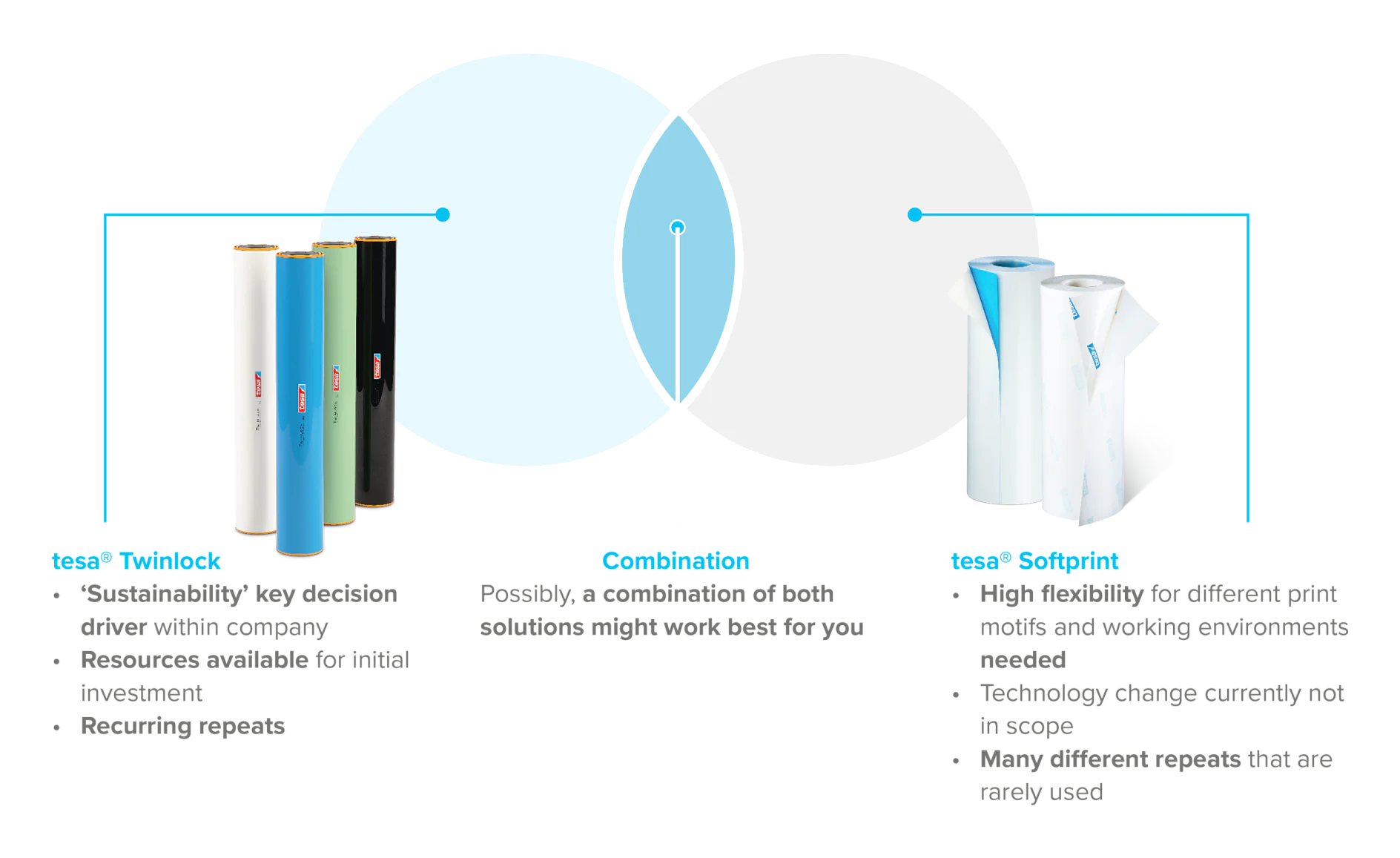
Have further questions? Reach out to our tape experts today!