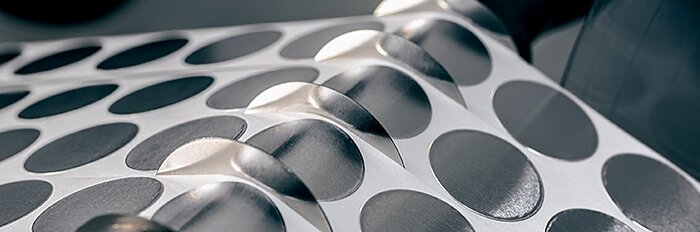
Covering holes in car bodies: An adhesive solution
Technologies
One. Two. Three. Four…
Fifteen. Twenty. Twenty-five…
One hundred. One fifty. Two hundred…
It sure takes a long time to count all the holes in the body of a single car! Are there really as many as 220? In one car?!
Wow. That’s a lot of holes.
And here’s a little secret… the holes can’t stay in the car body forever! What?!
It’s true. Read on to find out why. And to learn what tesa® is doing to solve this complex hole covering issue the automotive industry deals with all the time.
Why does a car body have so many holes?
That’s something our tape nerds would love to answer for you, so thanks for asking!
Car bodies have a whole lot of holes for a whole lot of reasons. Here are a few of them:
• Assembly - Some openings make it easier for manufacturers to assemble hard-to-reach parts.
• Transport - Others serve the manufacturing process well, making it easier to move vehicles from one location to another during assembly.
• Corrosion Protection - Some aid the dip-coating process by allowing the corrosion-protective coating to flow throughout the body, ensuring complete coverage.
The tricky part is—those holes can’t stay open forever. They’d let too much dirt and moisture into finished cars and create turbulence noise that might make drivers crazy as they drive down the interstate.
Instead, manufacturers have to cover the holes, and they often do that with plastic, rubber, or metal plugs using a process that takes a lot of people, time and hard work to precisely plugs into every single hole.
Every. Single. Hole. You read that right!
There’s no one-size-fits-all with conventional plugging. Every opening has to have a unique plug geometry to fit exactly and be pushed in with just the right force for the plug to actually work.
Advantages of Adhesive Hole Coverings
So what if we told you we have some really great news for you? What if we said that conventional plugging is no longer the only option?
Well… Guess what? It isn’t!
Self-adhesive patches are changing the game! They come in various sizes and designs and offer decisive advantages over conventional plugs. While conventional plugs have to fit exactly, adhesive hole coverings can close holes that are completely different sizes… with a one-size fits all stamped part.
Didn’t we tell you this was great news? It saves so much time. And definitely cuts down on the complexity.
Adhesive die cuts also rescue your production workers because they don’t have to worry about how much pressure they’re putting on the plugs. They simply press the adhesive coverings on and keep rolling.
And we’ve got to tell you, besides being simpler, saving time, and reducing effort, the simple switch to adhesive hole coverings actually saves the manufacturers money. Because the die cuts are lighter than conventional plugs, the car bodies are also lighter, which means they use less fuel… and owners can put that cash right back in their pockets!
Who wouldn’t be happy about that? We definitely are.
We’re also pretty stoked about the other advantages adhesive hold coverings provide. Things like impermeability, heat resistance, noise reduction, and puncture resistance.
Bottom line? They’re an all-around win for the automotive industry.
Adhesives and Automation
Thinking ahead to how well adhesive hole coverings work in an automated setting, we’ve got to say robotic applicators can apply them super-fast in a fully automated system.
And having robots do the work of placing the adhesives in hard-to-reach places may keep production workers healthier because they won’t have to worry about the ergonomics of straining in strange and uncomfortable positions.
Want to learn more about adhesive coverings that save time, effort, and money? Visit our hole covering solution page!