The Porsche models from the automobile manufacturer's main plant in Stuttgart-Zuffenhausen have always been considered the flagships of modern engineering. Some automotive journalists were surprised when Porsche AG announced that they had developed an innovative production process together with tesa. Would this mean that from now on the stylish sports cars will be glued together? That's what attentive readers suspected in mid-April when they saw the headlines of well-known specialist and consumer magazines. The answer is: Yes, but not with the popular tesafilm®.
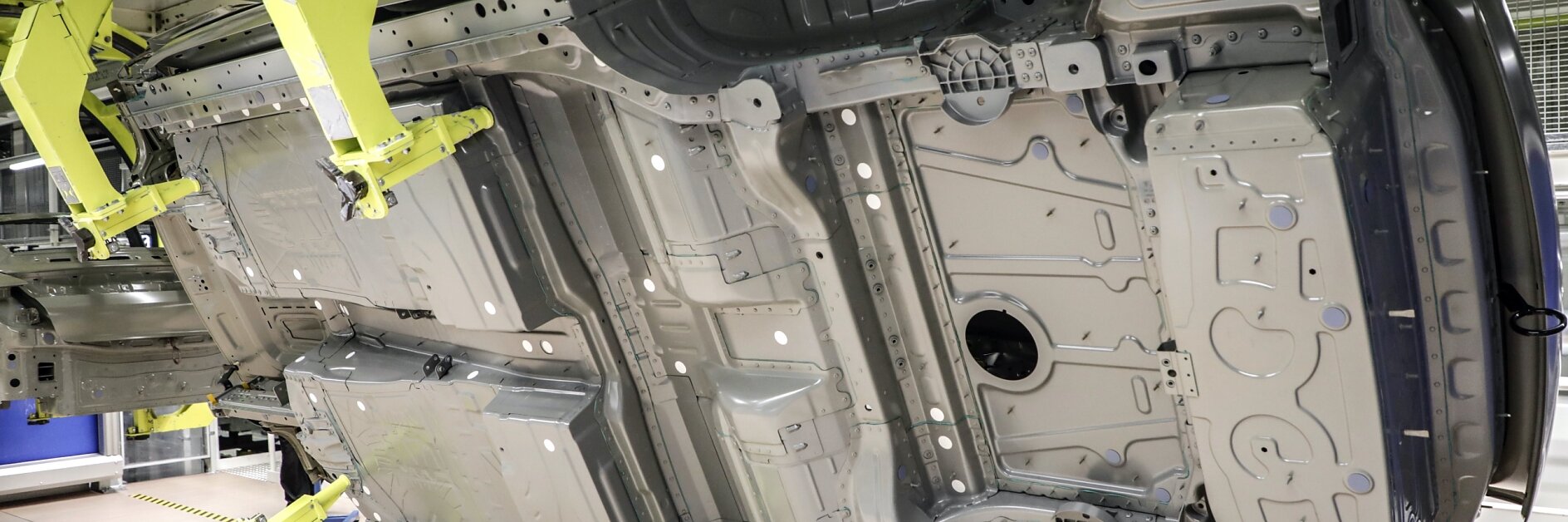
Patch instead of plug - Close cooperation with Porsche
Markets
These days, a collaboration between two world brands is nothing special. However, the news that Porsche will not be cooperating with Tesla in the production of its prestigious Taycan electric model, but rather with tesa, surprised many from the "automotive scene". Special adhesive patches are used for the robot-assisted hole covering on car bodies.
10 billion holes in car bodies
Every year worldwide more than 10 billion holes in car bodies – necessary for the e-coat painting process – must be covered for corrosion protection. Often, this task is still performed by hand using plastic plugs – an extremely time-consuming, straining and personnel-intensive process. The alternative: Adhesive patches from tesa (opens in a new window or tab) that a robot applies quickly and reliably.
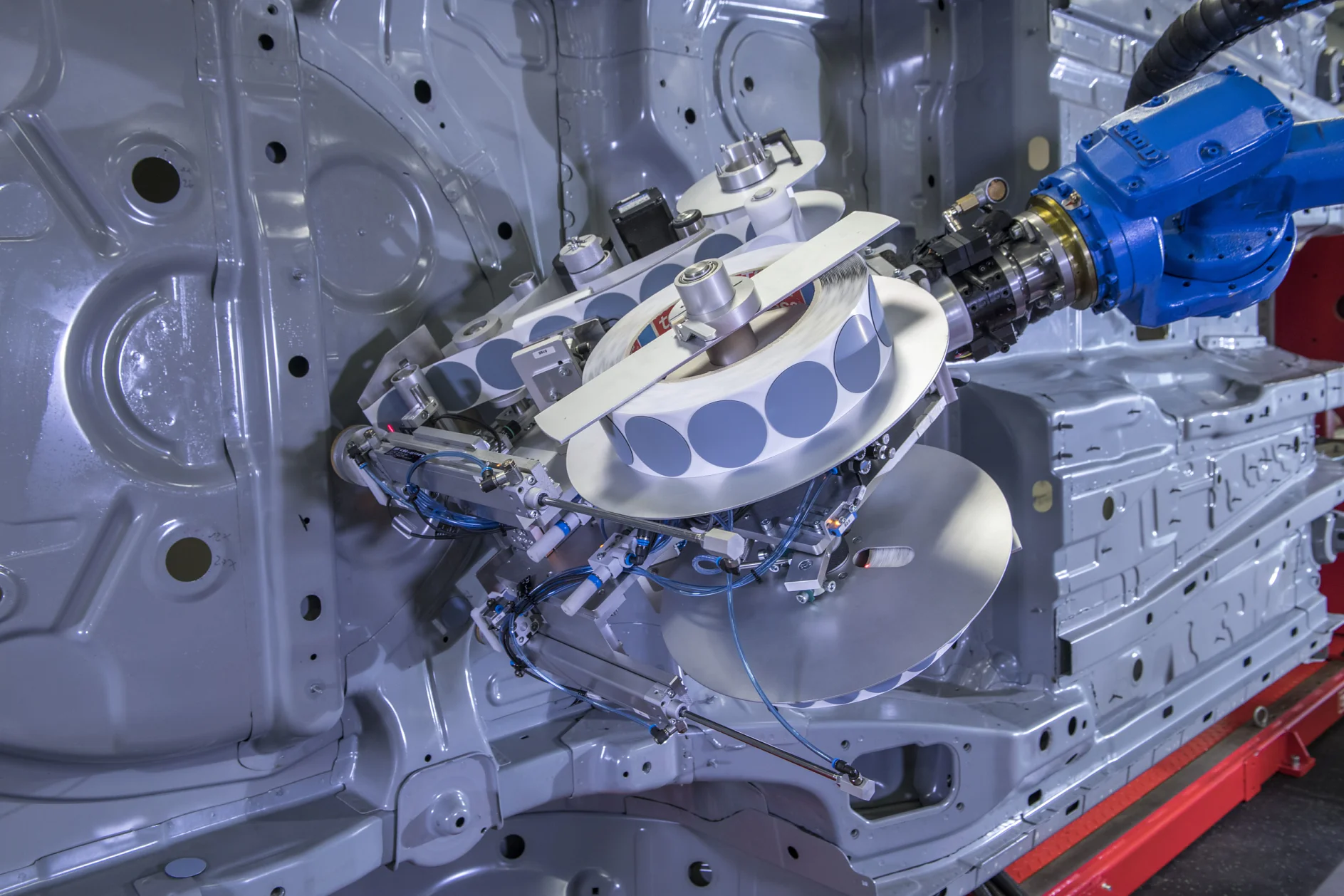
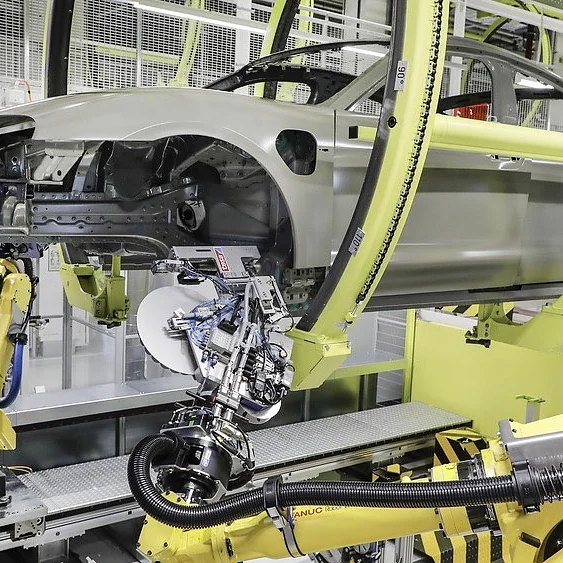
Close cooperation with engineers
Porsche AG, together with their long-term supplier tesa, has developed an innovative robot-assisted manufacturing process at their headquarters in Zuffenhausen. The fully electric Porsche Taycan is the first vehicle in the world to use this new automation technology that optimizes hole covering and thus the entire production. "Innovations have always been the engine for our economic success," says Albrecht Reimold, Board Member Production and Logistics at Porsche AG. “New innovations have to be mastered. This requires courage and creative freedom." By summer 2021, Porsche AG will implement this new concept also in their paint shop at the Leipzig plant.
"The positioning accuracy is significantly higher compared to the manual process: 100% effectiveness in half the time."
Corporate Vice President tesa Business Unit Automotive
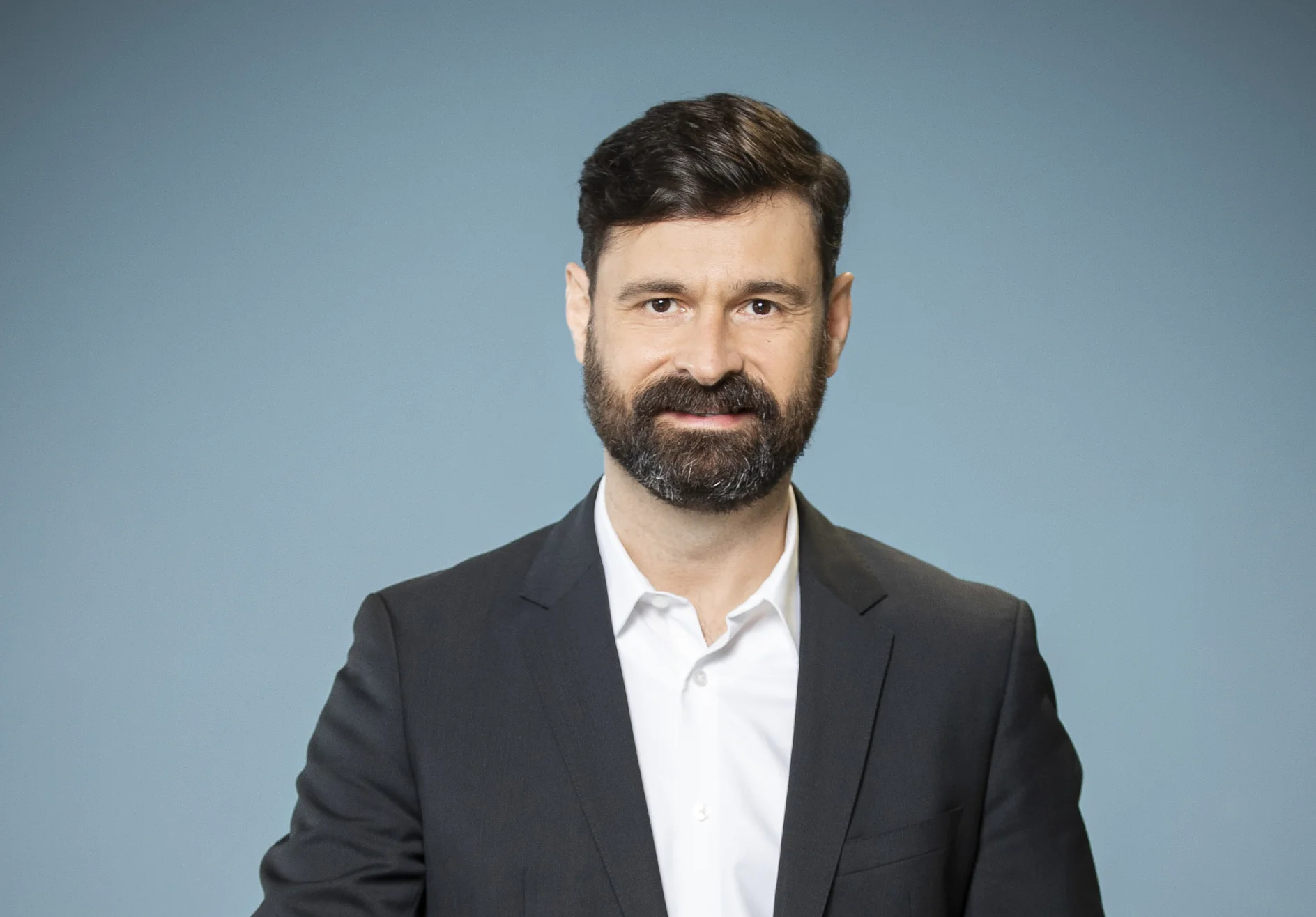
An adhesive tape that works like a "fire brigade"
Compared to conventional plastic plugs, the tesa® sealing patches feature a variety of advantages. While the plugs always have to fit perfectly, it is possible to cover holes of different widths with one defined patch size by overlapping. This reduces the overall complexity and saves time. In addition, tesa® adhesive patches also offer extra benefits. The base product, tesa® PunctureGuard ensures corrosion protection via perfect sealing combined with high mechanical strength and good noise dampening properties.
Furthermore, these durable adhesive patches that are only one millimeter thin yet extremely tough (they last a car life), are significantly lighter than the approximately six-millimeter plastic plugs. This is of great relevance for e-cars, as every extra gram means a loss of range. Our special product tesa® FireGuard, developed for the so-called Battery Foot Print (thus, for the use with electric batteries), withstands flames of up to 500 degrees Celsius for six minutes, protecting the passenger compartment to allow driver and passengers to get out of the vehicle in case a defect battery catches fire.
25,000 KG
is the weight that workers have to move with their thumbs per shift to push approx. 3,500 conventional plastic plugs into the holes of car bodies – an enormous ergonomic strain.
Flexibility and speed thanks to robots
"Our automatic application unit, tesa® EfficienSeal, was developed utilizing tesa expertise and guarantees the expected quality of the sealed hole," explains David Caro, Corporate Vice President of the tesa Business Unit Automotive. With the use of innovative automation technology, tesa customers in the automotive industry enjoy a high degree of flexibility: Depending on the vehicle type – and on the related placement and number of holes in the body – the robot can apply different patches as needed by quickly changing the application heads.
Like Swiss cheese ...
... that's what a car body looks like in the production hall. But where do all these holes come from – on some models there are more than 200 – and what is their function? Some holes allow the assembly of components that are difficult to access or are used for transport purposes. For the most part, the holes are required in the dip painting process so that the paint can reach all corners and then flow off, thus, guaranteeing full corrosion protection. However, to stop moisture or dirt penetrating the car body holes in the finished new car as well as avoiding airstreams that may cause noise due to air turbulence, the openings must be sealed.