슈투트가르트-주펜하우젠에 소재한 포르쉐의 메인 플랜트에서 만든 포르쉐 모델들은 항상 현대 공학의 플래그십으로 생각되어 왔습니다. 일부 자동차 저널리스트들은 포르쉐가 테사와 함께 혁신적인 생산 프로세스를 개발했다고 발표했을 때 놀라움을 감추지 못했습니다. 스타일리시한 스포츠카가 이제부터 글루로 조립된다는 이야기일까요? 이것이 4월 중순 주의 깊은 독자들이 유명 전문잡지 및 소비자 잡지의 헤드라인을 봤을 때 추측했던 내용입니다. 답은 그렇습니다. 그러나 인기제품 테사필름(tesafilm®)이 사용되지는 않습니다..
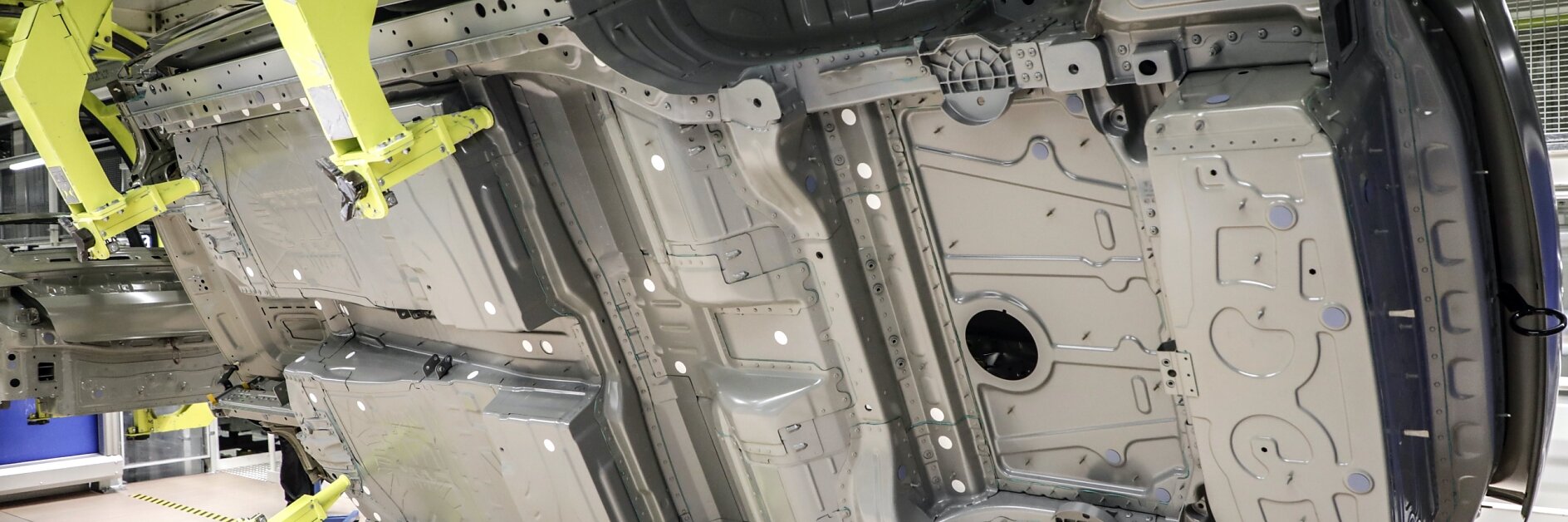
플러그 대신 패치 – 포르쉐와의 긴밀한 협력
시장
오늘날 두 개의 세계적 브랜드가 협력하는 것에는 특별할 것이 없습니다. 그러나 포르쉐가 타이칸 전기차 모델 생산에 있어 테슬라와 협업하지 않고 테사와 협업할 것이라는 뉴스는 자동차업계의 많은 사람들을 놀라게 했습니다. 로봇 지원 자동차 바디 홀 커버링에 tesa의 특별한 점착패치가 사용됩니다.
자동차 바디에 있는 100억 개의 홀(구멍)
전세계에서 매년 자동차 바디에 뚫리는 홀은 100억 개 이상입니다. 이는 e-코트 도장 프로세스를 위해 필요한 홀인데, 부식 방지를 위해서는 커버링이 되어야 합니다. 플라스틱 플러그를 사용해 아직도 이 작업을 수작업으로 수행하는 경우가 많습니다. 이렇게 하면 상당히 많은 시간을 요하고 차량 바디에 부담이 가고 인력 소모가 큽니다. 그 대안으로: 테사의 점착 패치 (opens in a new window or tab)를 로봇이 빠르고 신뢰성 있게 적용할 수 있습니다.
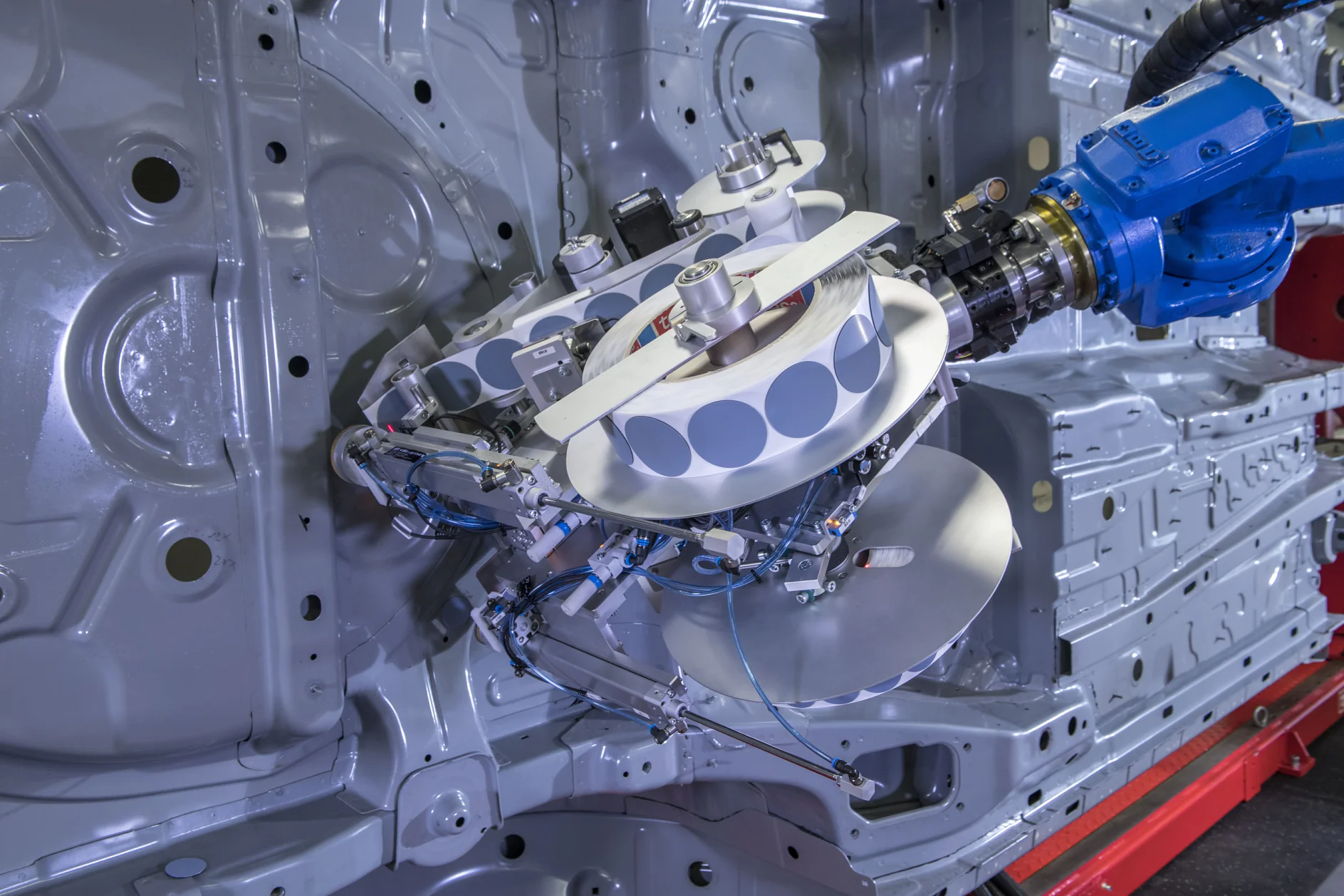
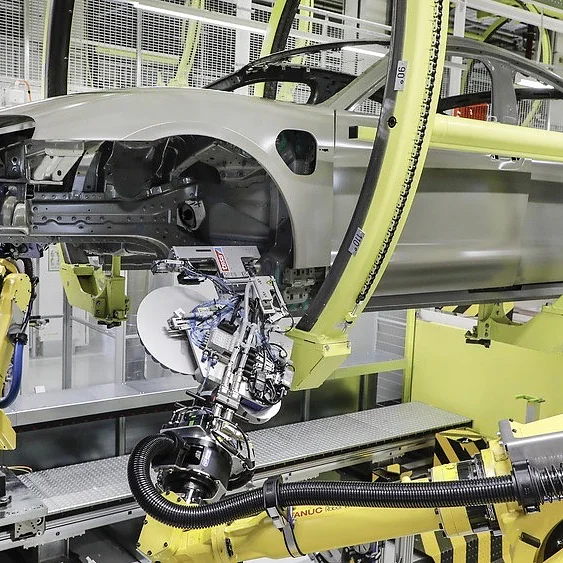
엔지니어와 긴밀한 협력
포르쉐는 오랜 기간 공급자였던 테사와 함께 주펜하우젠에 소재한 본부에서 혁신적인 로봇 지원 제조 프로세스를 개발했습니다. 전기차인 포르쉐 타이칸은 세계 최초로 홀 커버링을 최적화하는 이 신 자동화 기술을 사용해 전체 생산을 자동화한 케이스입니다. 포르쉐의 Board Member Production and Logistics Albrecht Reimold는 “혁신은 언제나 우리의 경제적 성공을 이끈 원동력이었습니다.”고 밝혔습니다. “이러한 새로운 혁신에 숙달되기 위해서 용기와 창의적인 의지가 필요합니다.” 포르쉐는 2021년 여름까지 라이프치히 플랜트의 도장 샵에서도 이 새로운 개념을 시행할 예정입니다.
"수작업 대비 포지셔닝의 정확성이 크게 높아져, 절반 정도의 시간에 100%의 효과를 낼 수 있습니다."
Corporate Vice President tesa Business Unit Automotive
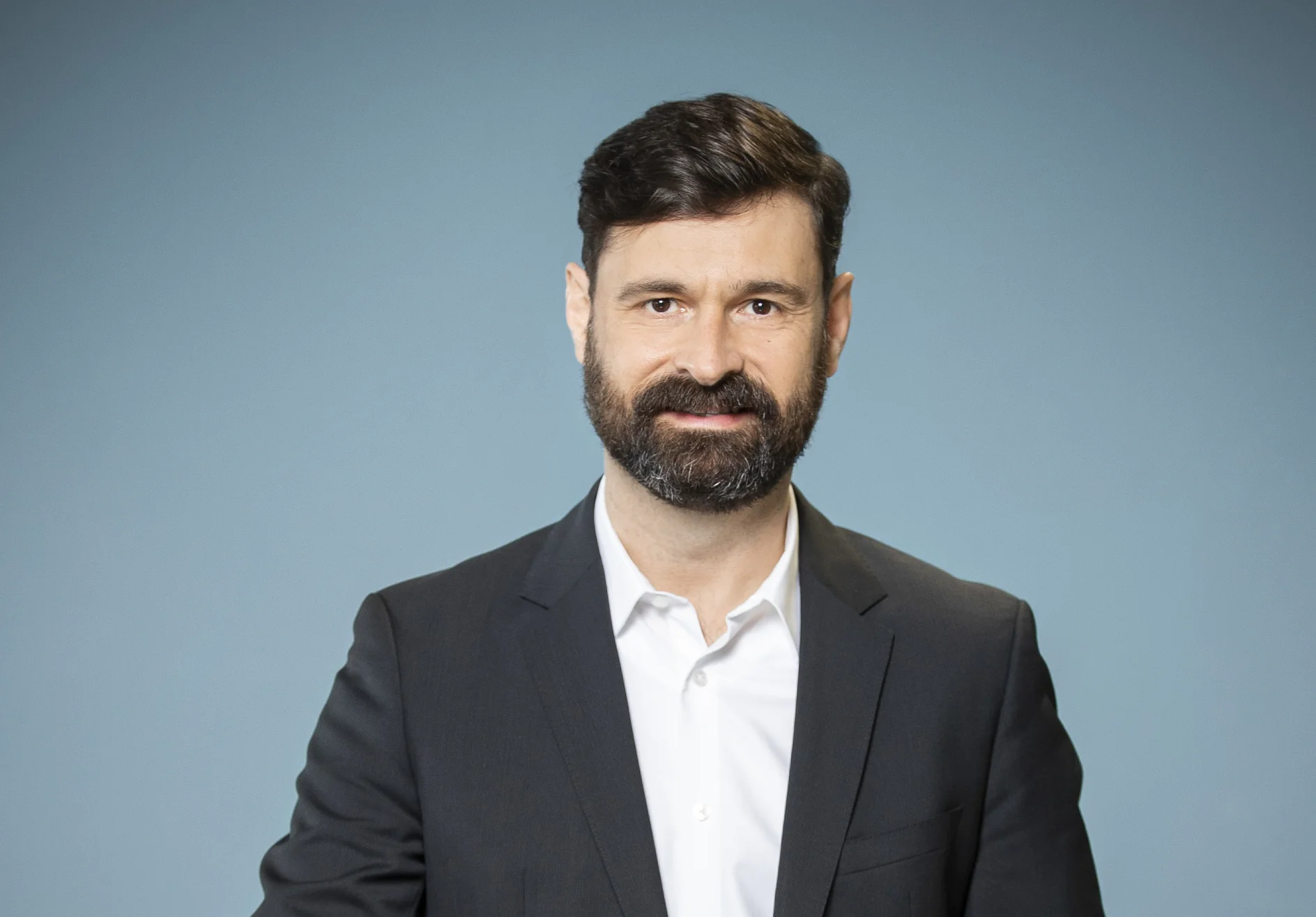
소방대와 같은 기능을 제공하는 점착테이프
재래식 플라스틱 플러그와 비교했을 때 테사 실링패치는 다양한 장점을 갖습니다. 플러그는 언제나 완벽하게 꼭 맞아야 하지만, 패치는 겹쳐 붙일 수 있기 때문에 한 가지의 정해진 패치 사이즈로 여러 직경의 홀을 커버링할 수 있습니다. 이는 전반적인 복잡성을 줄여주고 시간을 절약해 줍니다. 또한 테사 점착패치는 추가적 장점도 가져다 줍니다. 베이스 제품인 테사 펑처가드(tesa® PunctureGuard)는 완벽한 실링과 높은 기계적 강도, 훌륭한 소음 감소 기능으로 부식을 방지해 줍니다.
또한 이 내구성이 좋은 점착패치는 겨우 1mm 두께지만 놀라울 정도로 튼튼하고(자동차 수명만큼 오래 갑니다.) 약 6mm의 플라스틱 플러그 대비 훨씬 가볍습니다. 이는 전기자동차에는 큰 의미를 갖습니다. 차 중량이 1그램 더 나갈 때마다 주행거리가 줄어들기 때문입니다. 배터리 풋 프린트(Battery Foot Print, 전기 배터리 사용)를 위해 개발된 테사의 특수 제품 테사 파이어가드(tesa® FireGuard)는 6분간 최고 500도의 화염에서 견딜 수 있어 승객실을 보호하여 운전자와 승객이 결함 배터리로 인한 화재 시 차량에서 탈출할 수 있게 해 줍니다.
25,000 KG
약 3,500개의 재래식 플라스틱 플러그를 자동차 바디의 홀에 끼워넣기 위해 각 교대 당 엄지손가락으로 움직여야 하는 중량입니다. 이는 막대한 인체공학적 부담입니다.
로봇으로 유연성과 속도 개선
Corporate Vice President of the tesa Business Unit Automotive의David Caro는 “테사의 자동차 애플리케이션 유닛인 테사 이피션실(tesa® EfficienSeal)은 테사의 전문지식을 활용해 개발되었으며, 실링된 홀의 기대 품질을 보장한다.”고 말합니다. 자동차업계의 테사 고객은 혁신적 자동화 기술을 사용해 고도의 유연성을 누릴 수 있습니다. 차량 유형에 따라, 그리고 바디의 홀의 위치와 수에 따라 로봇이 빠르게 애플리케이션 헤드를 바꿔 필요한 여러 패치를 적용할 수 있습니다.
Like Swiss Cheese
... 생산 작업장에서 자동차 바디의 모습입니다. 그러나 이 모든 홀이 어디서 왔을까요? 일부 모델에는 200개가 넘는 홀이 있습니다. 그리고 이 홀의 기능은 무엇일까요? 일부 홀은 접근하기 어려운 부품의 조립을 가능하게 하거나, 운송 목적에 사용됩니다. 대부분의 부품은 딥 도장(dip painting) 공정에서 홀을 필요로 합니다. 페인트가 모든 코너에 도달하여 흘러나가 완전한 부식 방지가 되도록 하는 것입니다. 그러나 완성된 신차에서 자동차 바디 홀에 습기나 오염물이 침투하는 것을 막고, 에어 터뷸런스로 인해 소음을 유발할 수 있는 에어스트림을 피하기 위해서는 개방부를 실링하여야 합니다.